Fiber carding machine is a piece of industrial fiber recycling equipment used in textile manufacturing. Its main function is to loosen and comb the fibers into a form suitable for further processing through the process of opening, carding and removing impurities. Fiber carding machine can process raw materials such as chemical fiber, linen spinning, cotton spinning, wool spinning, textile waste yarn, waste clothing, textile trimmings, non-woven fabrics and so on.
Features of Fiber Carding Machine
- Powerful opening and fine carding. Through the high-speed rotating stab rollers and rollers, it can effectively loosen the fiber clumps. And after many times of carding, fibers become softer and neater, suitable for subsequent processing.
- Efficiently removing impurities and dust. Adopting high-power suction fan, it can effectively remove the dust and fine impurities in the fiber to ensure the cleanliness of the fiber.
- High degree of automation. It is equipped with advanced control system, easy to operate, with one-key start, automatic shutdown and other functions.
- Versatility. It can handle many types of fiber raw materials, including chemical fiber, linen, cotton and so on.
- Easy maintenance. The machine is upgradable, so it is easy to replace the wearing parts such as blades and spiked rollers, which reduces the maintenance cost.
- Support customization. Customers can customize the number of rollers and the installation of the fence according to the demand. The more the number of rollers, the better the effect of processing materials.
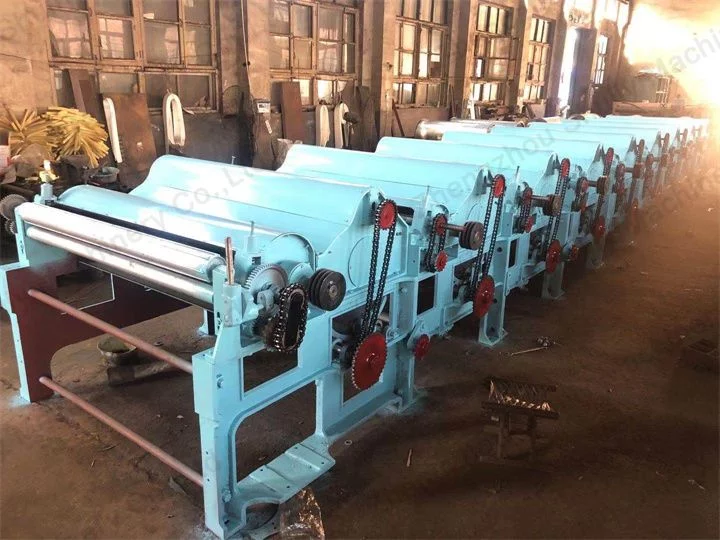
Structure of Textile Carding Machine
- Frame: the support structure of the fiber carding machine. Made of steel with good stability and durability.
- Feeding device: the fiber material to be treated is fed into the machine through the conveyor belt.
- Opening system: it is the heart of the machine. Inside there are several cleaning elements (e.g. cleaning needles, rollers, etc.), which are used to loosen the fibers further and comb the fibers to remove the impurities in them.
- Dedusting system: it is used to generate airflow to separate and collect the cleaned impurities and dust to ensure the purity of the fibers after cleaning.
- Control system: it is equipped with an electrical control cabinet to monitor and control the operation of the blow room. It is also equipped with safety protection devices to ensure the safe operation of the equipment.
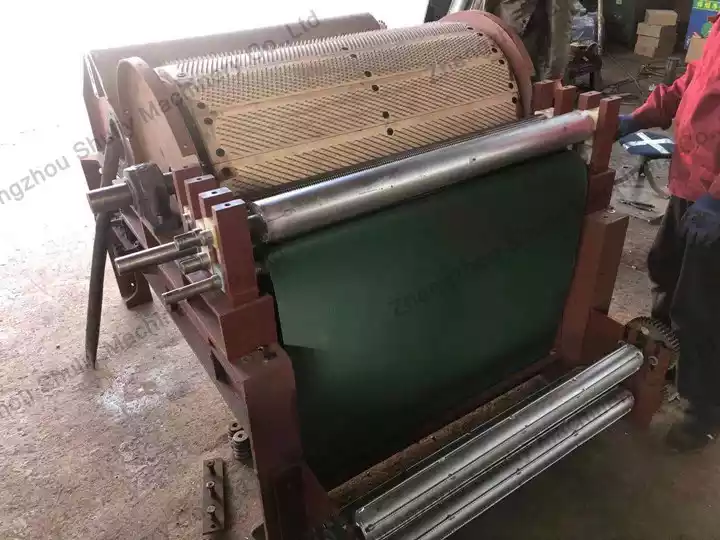

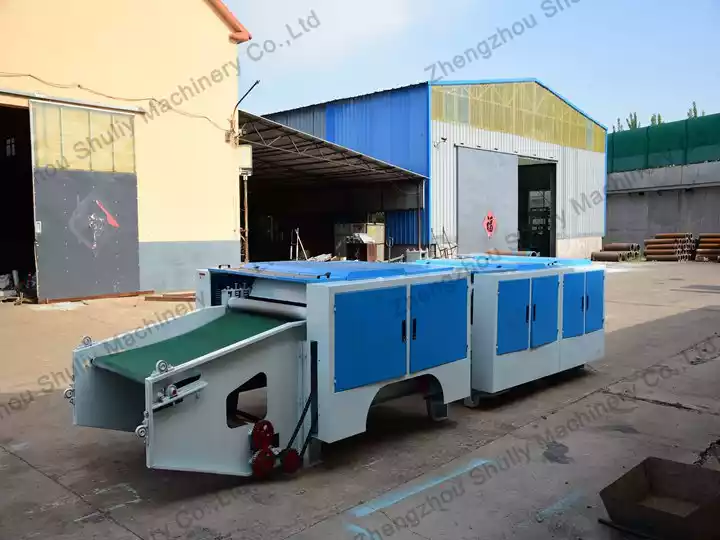
How Does A Fiber Carding Machine Work?
Material Preparation
Feed the raw materials to be processed (e.g. waste garments, waste yarns, etc.) into the feed opening of the fiber carding machine.
Opening
In the first step, the raw material is fed into the inside of the machine by means of a transportation belt.
In the second step, the raw material is unfolded by the rotating rollers to initially loosen the fiber clumps.
In the third step, the high-speed rotating felting roller is equipped with dense fine crochet needles. The fibers are further loosened by the action of the barbs and needles, making them loose.
Carding
The loosened fibers are shurried and further removed from the impurities therein by means of a dust cage. The impurities are then removed from the fibers by means of a debris removal plate.
Cleaning
Adopt high-power suction fan or other dust removal equipment to discharge the dust and impurities in the fiber to ensure the cleanliness of the fiber.
Output
Outlet plate under the pressure and rotation of the dust cage and the calender rollers. It is then collected and baled.

Models of Fiber Carding Machine
Model | Capacity(kg) | Power(kw) | Size (mm) | Roller length(mm) | Roller dia(mm) | Weight(kg) |
SL250B | 150-250 | 11 | 2000X1700X1300 | 1000 | 250 | 800 |
SL250B-2 Roller | 150-250 | 29 | 2900X1700X1300 | 1000 | 250 | 1500 |
SL250C-3 Roller | 150-250 | 34 | 4000X1700X1300 | 1000 | 250 | 2350 |
SL250D-4 Roller | 150-250 | 40 | 5100X1700X1300 | 1000 | 250 | 3200 |
SL250E-5 Roller | 150-250 | 45.5 | 6200X1700X1300 | 1000 | 250 | 4050 |
As you can see from the parameter table, we have many different types and outputs of roller carding machine for sale. If you are interested in a particular machine, you can contact us.
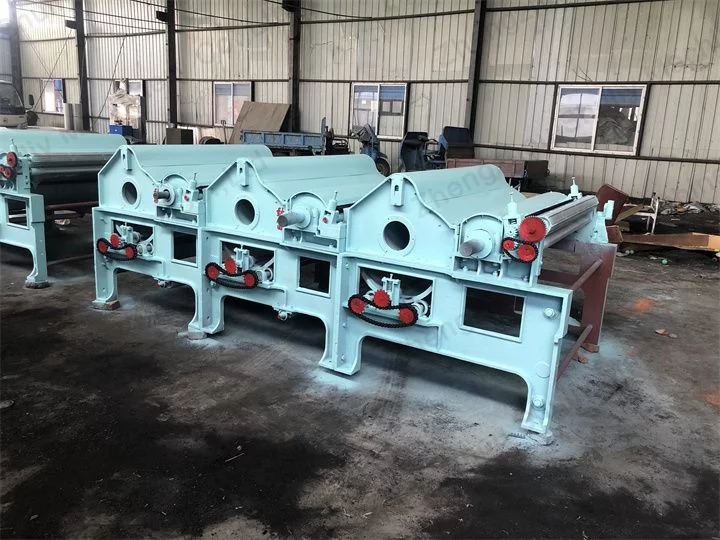
Price of Cotton Carding Machine Price
Basic, smaller capacity cotton carding machines designed for small-scale operations may cost a few thousand dollars. Larger, more advanced models used in industrial settings can cost tens of thousands of dollars or more.
To get an accurate and up-to-date price for a cotton carding machine, I recommend contacting professional roller carding machine manufacturers directly. We can provide you with current pricing information and details about specific models that meet your requirements. Additionally, you can compare prices from multiple sources to find the best deal for the machine that suits your needs.
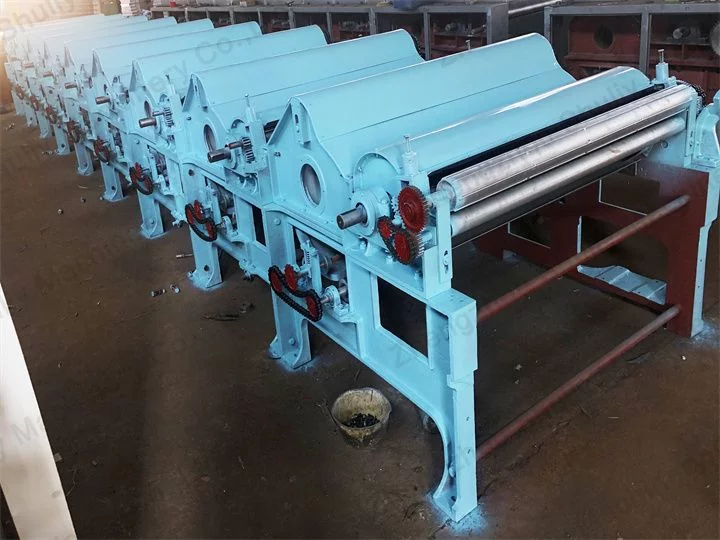
Reliable Fiber Carding Machine Manufacturer
- A wide range of fiber recovery equipment is available. Shuliy Recycling Machinery is a reliable manufacturer specializing in the research and development of textile recycling machinery. We offer a wide range of textile recycling machines, including fiber opening machines, fiber cutting machines, textile balers, and so on.
- Increasing number of global cooperative customers. As a professional and experienced cotton carding machine manufacturer, our machines have been exported to more than 30 countries and regions around the world.
- Customized services. We also provide unique customized services for different customers’ needs. If you are looking for high-quality machines, please feel free to contact us, and we will contact you as soon as possible.
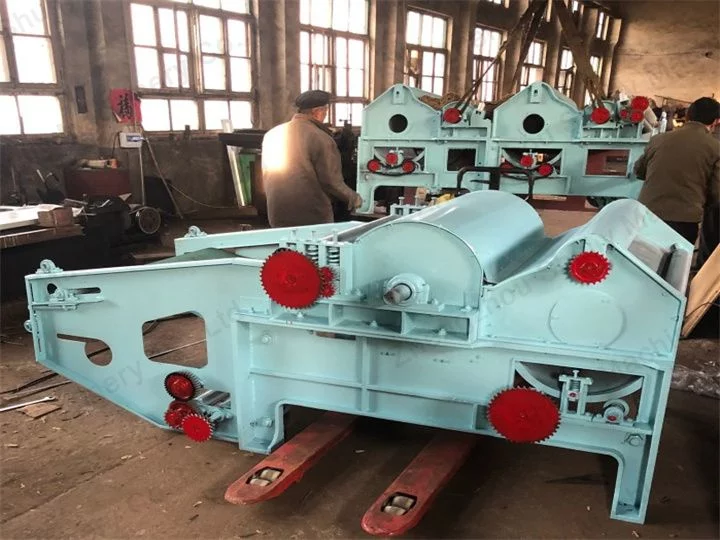
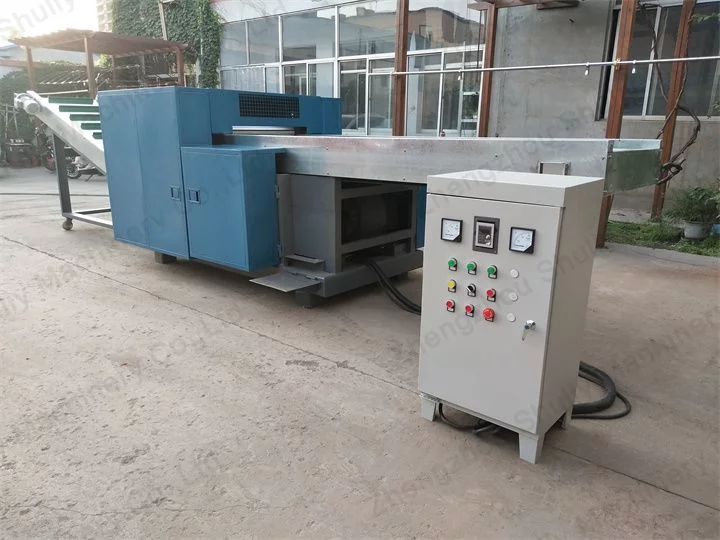
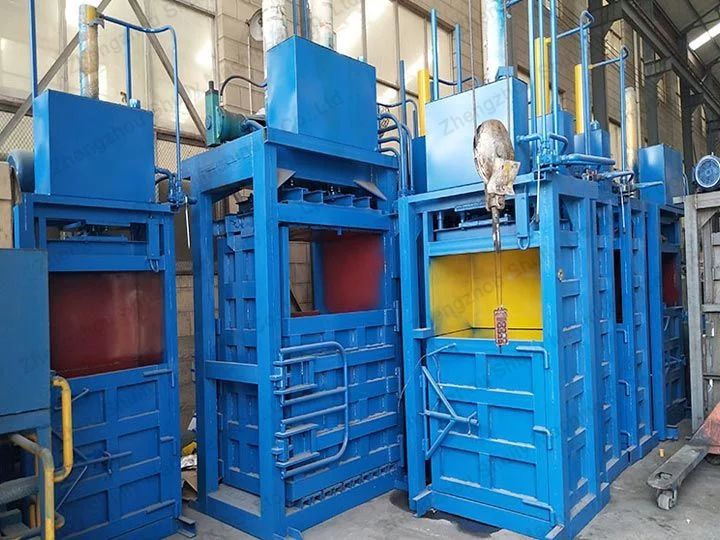
Fiber Carding Machine Applications
Fiber carding machines find extensive applications in the textile industry, where they are employed to process various raw fibers, such as cotton, wool, and synthetics, ensuring uniformity and alignment before spinning into yarn.
Additionally, these textile recycling machines are vital in non-textile industrial settings for recycling applications. In the mattress and bedding industry, wool carding machines are used to create cushioning materials. Furthermore, they play a key role in automotive manufacturing, providing insulation and soundproofing materials.
In summary, drum carding machine is versatile. It can be used in a variety of industries such as the textile industry and the recycling industry. In these industries, precise alignment and preparation of fibers is essential to produce a quality end product.
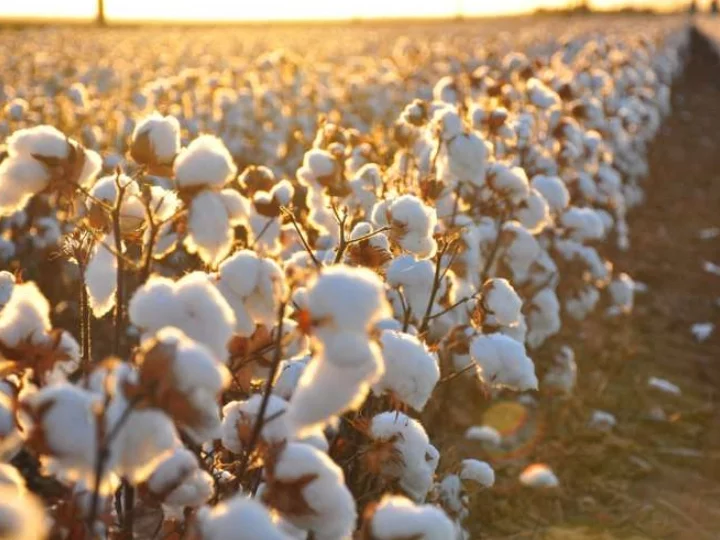
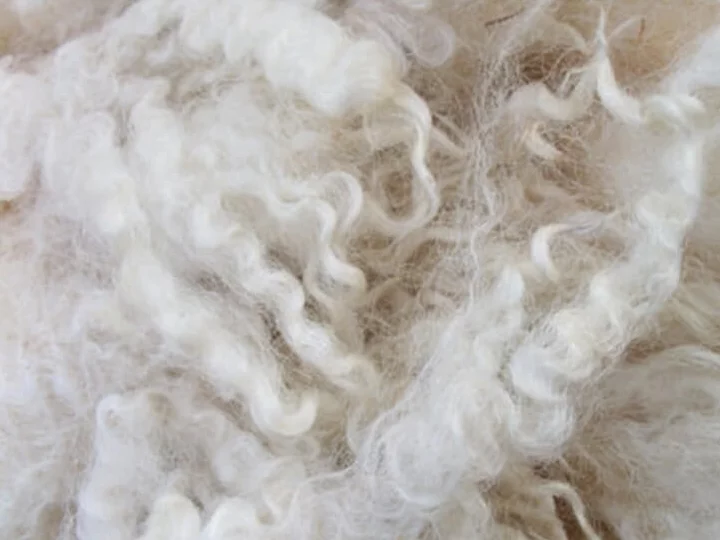
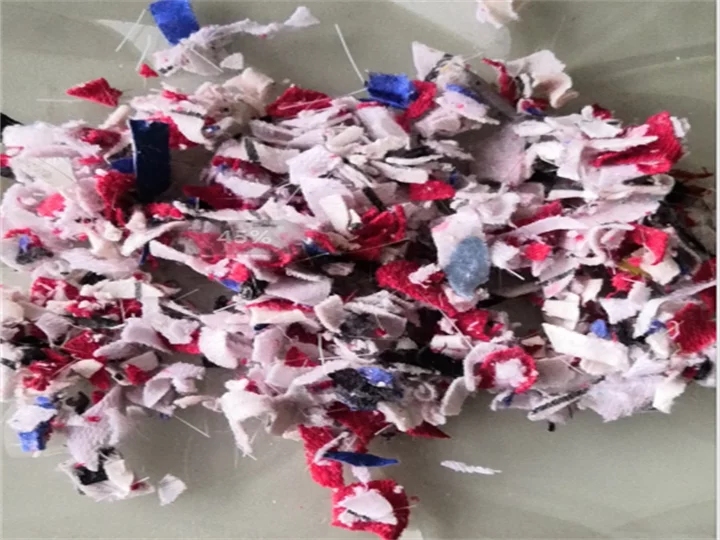
Main Faults of the Machine and Troubleshooting Methods
Quality of Finished Products Cannot Meet the Requirements
First, check whether all the spacing is adjusted to the specified requirements. Then check whether the rack on the stabbing roller has inverted teeth or is damaged.
Fiber Contains More Impurities
Duct obstruction or fan outlet exhaust difficulties lead to short fluff or dust that can not be sucked out in time and mixed in the fiber. At this time, you should check whether the air duct or fan outlet is blocked and clean up the fleeces and dust in time.
Machine Noise
The vibration of the whole machine may be caused by the unevenness of the installation foundation or the loosening of the positioning bolts of the frame. It is also possible that the bolts fixing the bearing seat of the stab roller are loose. We just need to tighten the bolts.
Chain Falling Off
The sprocket is not in a straight line due to the misalignment of the sprocket installation. Adjust the position of the sprocket can be solved.