An EPS compactor, also known as a polystyrene compactor or styrofoam densifier, is an important machine in the waste foam recycling industry. With the help of the Shuliy’s EPS foam compactor, the volume of foam can be reduced up to 40 times by cold pressing. What’s more, it is very energy efficient and environmentally friendly while efficiently reducing the volume of waste foam.
Feature of the Styrofoam Densifier
- Cold compression technology. Shuliy’s EPS foam densifier utilizes cold compression techniques to condense expanded polystyrene efficiently, reducing its volume significantly without the need for added heat, making it environmentally friendly.
- High compression ratio. These polystyrene compactors offer an impressive compression ratio, often achieving ratios of 40:1 or higher, ensuring substantial reduction in EPS foam volume, and simplifying storage and transportation.
- Adjustable compression ratio. There is a pressure-adjusting device at the front of the EPS compactor machine, so customers can adjust the compression ratio according to their needs.
- Durable construction. Styrofoam densifiers are built with durable materials and reliable components, ensuring longevity and consistent performance even in demanding industrial environments.
- Energy saving and environmental protection. By compressing the foam into blocks through the machine, it not only saves space for storage and transportation, but also improves the recycling rate of waste foam.
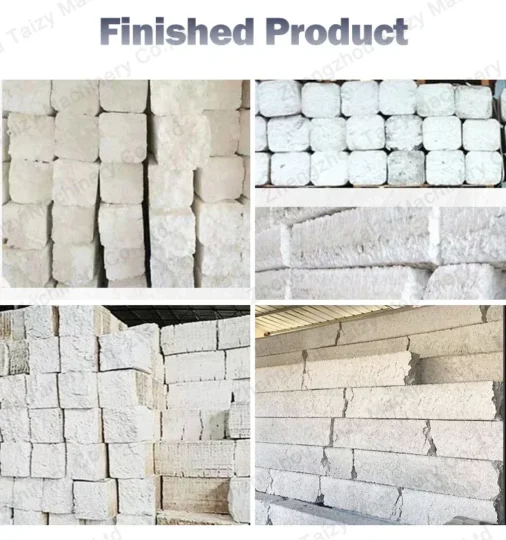
Application Scenarios of Foam Densifier
- Packaging industry. Used for compressing and baling waste foam materials generated during the production process to improve warehouse utilization.
- Manufacturing industry. Used for compressing and baling waste foam materials generated during the production process to facilitate waste management.
- Retail industry. Used for compression and baling of waste foam materials generated in the transportation process to facilitate recycling.
- Logistics centers. For compression and baling of waste foam materials generated during the logistics process to facilitate transportation and storage.
How Does an EPS Compactor Work?
- Feeding: put the styrofoam waste to be recycled into the feeding port.
- Crushing: the crusher device will shredder the large pieces of foam into small pieces.
- Cold pressing: the cold press device of the foam compactor machine will compress the crushed waste foam. Unlike the foam melting machine, the foam densifier machine will not generate heat during the working process.
- Squeeze out: the screw device extrudes the compressed polystyrene into square foam blocks.
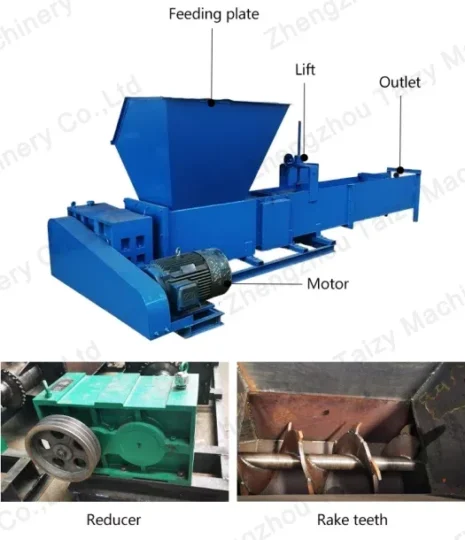
Best Polystyrene Compactor for Sale
The SL-300 model has a power output of 11 kw and a capacity of 150 kg/h. The inlet size measures 1100×800 mm, and the machine dimensions are 3000x1400x1400 mm.
In comparison, the SL-400 model features a power output of 22 kw and a capacity of 250 kg/h. The inlet size for this model is 1200×1000 mm, and the overall machine dimensions are 4600x1600x1600 mm.
Above are the technical parameters of two Shuliy recycling machinery‘s EPS compactor. Besides, we have other capacity EPS polystyrene densifiers for sale. If you want to know more detailed information about the equipment, including parameters, configuration, price, etc., welcome to contact us. We will surely contact you within 24 hours.
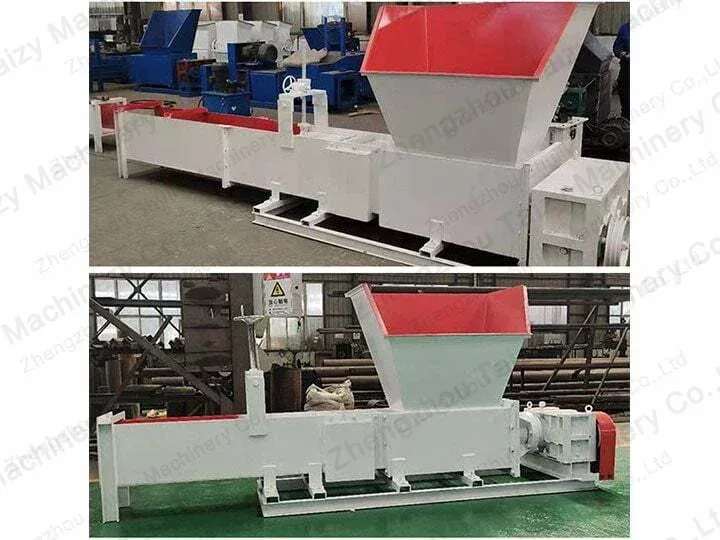
Styrofoam Densifier Cost
- Capacity and size. Larger styrofoam densifier equipment capable of handling higher volumes generally cost more than smaller units designed for lower quantities of Styrofoam.
- Technology and features. Foam densifiers with advanced features like automatic operation, higher compression ratios, or energy-efficient designs may be priced higher than basic models.
- Additional costs. It needs to consider additional expenses like shipping, installation, and any required accessories or maintenance plans.
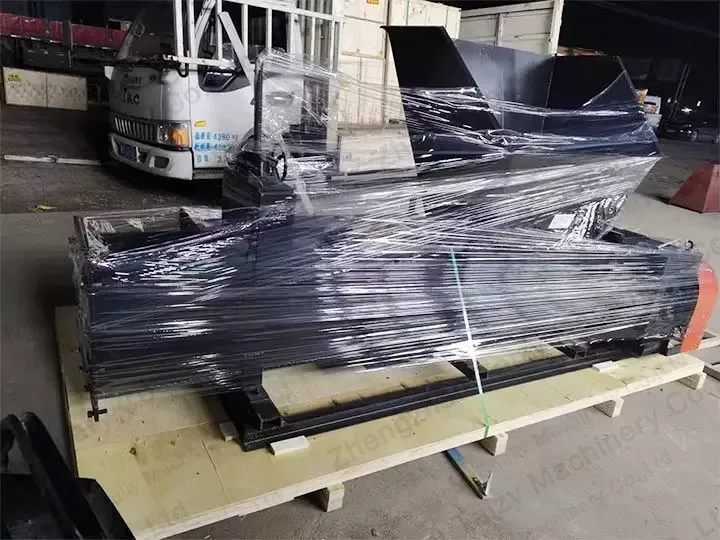
Types of Styrofoam Compactors
Cold Press Styrofoam Compactors
Using pressure without heat, these EPS styrofoam compactors compress waste foam into manageable blocks.
Screw Type Styrofoam Compactors
These screw type styrofoam compactor utilize a screw mechanism to compress polystyrene materials efficiently, often used in larger-scale operations due to their high throughput capabilities.
Hot Melt EPS Densifiers
Employing heat to melt expanded polystyrene, these plastic melter densifiers condense the material, creating denser blocks, and are favored for their effectiveness in reducing foam volume.
Hydraulic EPS Compactors
These hydraulic EPS compactors rely on hydraulic pressure to condense foam, providing versatility and adaptability in compressing various styrofoam densities.
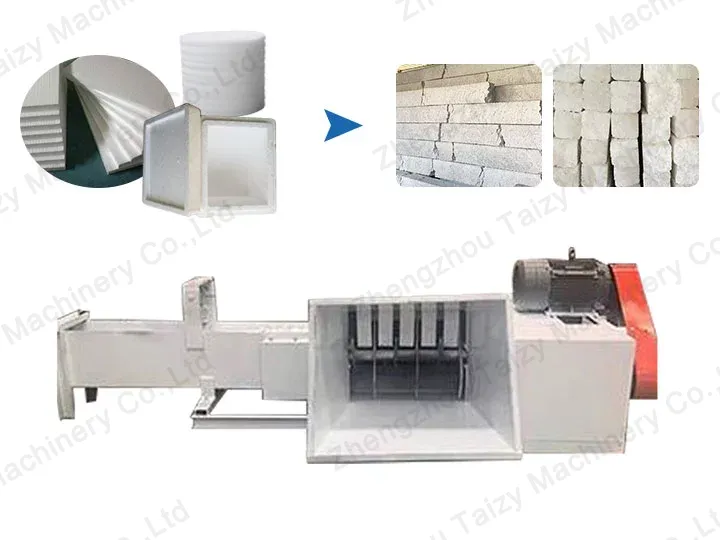
Maintenance and Operational Requirements of EPS Compactors
- Cleaning. Keep the machine clean from residual EPS foam and debris to prevent buildup that might hinder operation or cause damage.
- Safety checks. Regularly inspect safety features such as emergency stops, guards, and sensors to ensure they are functional for operator safety.
- Scheduled servicing. Schedule periodic servicing or professional inspections to address any potential issues before they become major problems, ensuring consistent functionality.
- Replacement of parts. Replace worn-out or damaged components promptly to prevent further damage to the machine and maintain optimal performance.
- Routine inspections. Conduct regular checks on key components such as hydraulic systems, electrical connections, and moving parts to ensure they’re functioning properly.
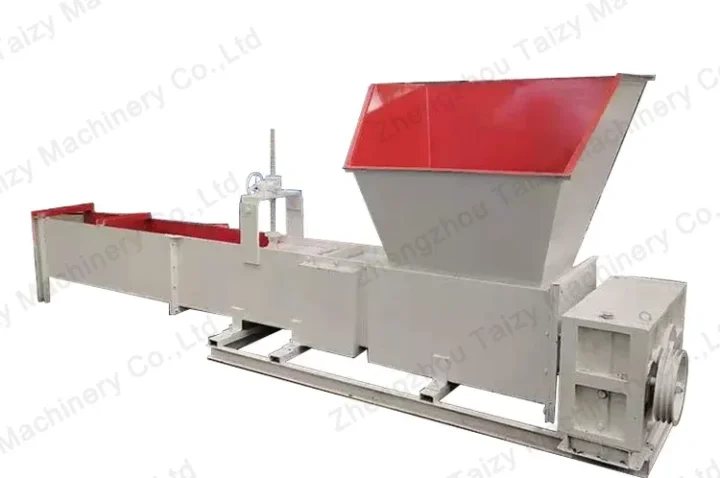